The accuracy of a sensor refers to the reliability of the measurement results, which represents the ability to repeat a certain reading with a given accuracy. The smaller the error, the higher the accuracy of the sensor [1].
The accuracy of a sensor is expressed as a percentage of the ratio of the maximum basic error within its range to the full range. The basic error is composed of two parts: systematic error and random error. System error is the difference between the average value obtained from infinitely multiple measurements of the same object under the same conditions and the true value of the object being measured. Random error refers to the difference between a certain measurement result and the average value obtained from infinitely multiple measurements of the same subject under repeated conditions [2].
The errors represented by hysteresis and linearity are the systematic errors of the sensor, while the errors represented by repeatability are random errors. The hysteresis characteristic indicates the forward (increasing input) and reverse (decreasing input) stroke outputs of the sensor; The degree to which the input characteristic curves do not coincide, as shown in Figure 1. Linearity refers to the degree of linearity between the output and input of a sensor, as shown in Figure 2. Repeatability represents the degree of inconsistency in the characteristic curve obtained by the sensor when the input quantity is continuously changed multiple times in the same direction across the full range, as shown in Figure 3.
So the accuracy of the sensorδ For:
In the formula, ∆ m— The maximum allowable basic error within the measurement range, yF ∙ S is the output full scale,δ L is linearity, i.e. non-linear error,δ H is hysteresis,δ R is repeatability.
In engineering technology, the concept of accuracy level is introduced to simplify the representation of sensor accuracy. The accuracy level is represented by a series of standard percentage values, such as the accuracy levels of pressure sensors being 0.05, 0.1, 0.2, 0.5, 1.0, 1.5, 2.5, etc. During sensor design and factory inspection, the error represented by its accuracy level refers to the maximum allowable error of sensor measurement.
2. Evaluation of Testing System Accuracy
A system is a collection or combination of several components or components. For example, detection
instrumentIt is a whole composed of detection components (sensors), conversion amplifiers, displays, and transmission channels, and has certain functions. Therefore, the detection instrument is also a system, and it can become a part of a larger automatic testing system or automatic control system. In terms of the testing system, the size of the system's error synthesis reflects its accuracy. Namely, the larger the comprehensive error, the lower the system accuracy, and vice versa, the higher it [3].
The final error of the system formed by the error balls of each link (detection component or instrument) in the testing system is the synthesis of the detection system error.
The accuracy of a testing system is determined by the system error and random error of the system. We know that system error is a constant or regular error, which is determined by the various sub system errors of the system. Single system error mainly depends on its nonlinearity, hysteresis, time drift, and other characteristics. System error can be avoided or reduced to a very small extent. And the random error, generally speaking, is irregular. But when measured multiple times, it still follows a normal curve distribution. Random error mainly depends on repeatability, and its characteristics are firstly, boundedness, where the absolute values of the error are within the limit error range. 2、 Unimodal, errors with small absolute values occur more frequently than errors with large absolute values. The third is symmetry, where positive and negative errors with equal absolute values occur approximately the same number of times. The fourth is compensation, where the limit value of the average error approaches zero as the number of measurements increases infinitely. This is very important when we analyze random errors [4]. The method of error synthesis is:
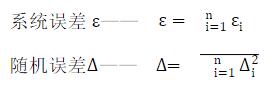
For a testing system error, it will be:
σ=ε+∆